
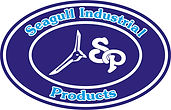
​​SEAGULL INDUSTRIAL PRODUCTS
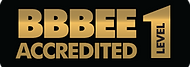
NYLON
The family of nylons consists of several different types. Nylon 6/6, nylon 6, nylon 6/10, nylon 6/12, nylon 11, nylon 12, and nylon 6-6/6 copolymer are the most common. Of these, nylon 6/6 and nylon 6 dominate the market. The numbers refer to how many methyl units (-CH2-) occur on each side of the nitrogen atoms (amide groups). The difference in number of methyl units influences the property profiles of the various nylons. Moisture absorbance is decreased due to reduced polarity with further separation and less regular location of the very polar amide roups. Resistance to thermal deformation is lowered due to more flexibility and mobility in these methyl unit sections of the main chain. As these units increase in length, making the molecules appear more like polyethylene, the properties of the nylon shift slightly toward those of polyethylene. Not considering the effects of moisture, Nylon 6/12 has lower modulus, higher elongation, lower strength, lower thermal distortion temperature, lower hardness and lower melting point than nylon 6/6. One relationship which does not conform is price. Nylon 6/12 is more expensive than nylon 6/6. The property which gives nylon 6/12 its utility is moisture absorption which is approximately half of that of nylon 6/6. This means the properties are much more consistent and experience less fluctuation due to ambient humidity levels in the end application.
Moisture absorption by nylon has been a source of great study for many years. Although all polymers absorb some amount of moisture, on none does it have such a significant effect as on nylons.

Water molecules produce polar bonds with the amide groups in the nylon molecules. Although small, water molecules take up space and displace the nylon molecules. This results in the nylon molecular matrix swelling. Dimensional changes of 0.7% can result in nylon parts from the "as-molded" state to equilibrium at 50% R.H. environments. This change occurs in approximately 150 days for a 0.0 60 inch (1.5 mm) thick part. (Ref 17) Molecular mobility is increased through the absorption of water. The increase in spacing between nylon molecules lowers the secondary forces allowing easier translational motion. This is the major reasons for the change in physical properties discussed above. There is less resistance to applied stress from the decrease in intermolecular friction. The change in molecular mobility is significant enough that molded nylon parts can relieve molded in stresses as they absorb moisture. Pretty neat 'eh?

The absorption of moisture by nylon is a completely reversible physical reaction. Drying in an oven will drive off all but a small percentage of the water molecules which can only be removed through dissolution of the nylon molecular matrix. The rate of absorption/desorption varies with type of nylon as well as temperature and relative humidity. Addition of fillers reduces the effect of moisture both due to volume reduction of the amount of nylon polymer in the mixture, and by sharing the attraction of the molecules somewhat reducing polarity and the available space for moisture molecules. Reinforcements reduce the effects more than fillers due to nylons strong affinity for reinforcement. In addition to the mechanisms which take place with fillers, the adhesion of the nylon molecular matrix to dimensionally stable reinforcements is stronger than than polar bonding of the water molecules and it dominates.

Another area where moisture has significant effects on nylons is in processing. Heated to molding temperatures while wet (ie., >0.2 % water) will result is hydrolytic degradation and a significant loss of physical properties. (Hydrolytic degradation is a chemical reaction which occurs at high temperature with some polymers in the presence of water. It causes primary bonds in the molecular chains to be severed thus reducing molecular weight.) Over drying (ie., <0.08% water) will remove the plasticizing effect of the water molecules and make the resin very viscous and hard to flow. The plasticizing effect in processing has to do with mobility and relative spacing of the nylon molecules, the same influence as on physical properties. This low level of moisture does not cause significant degradation during processing. The absorption of moisture by nylon must be considered in mold making. The shrinkage factor used in designing the mold must take the the potential for change in post molded dimensional into account. Although moisture causes problems in working with nylons, it does contribute to: better dyeability, toughness, softness and greater flexibility in nylon parts.
Another dominant feature of nylons is crystallinity. As with most crystalline polymers, the molecular chains are uncluttered by large substituent groups. They are flexible and regular in group spacing and crystallize readily. As with acetals, this crystallinity is responsible for properties of wear resistance, chemical resistance, thermal resistance, and unfortunately, higher mold shrinkage. The overall excellent property profile of nylons results in their probably having the most diverse range of applications of all thermoplastic polymers. Now let's talk about cutting nylon.
TIPS FOR MACHINING NYLON
STORAGE
Nylon has a high coefficient of thermal expansion (about three times that of aluminum) and low heat conductivity. Make sure that it has been exposed to normal room temperature for several hours before it is machined into finished parts.
SAWING
Nylon can be easily sawed on standard metal working equipment. Wood working equipment may be suitable but the high cutting speeds may cause excessive heat build-up. A blade that has been used for cutting metal is usually not sharp enough for nylon. Use a new coarse tooth blade with good set. Coolant may be used to control heat buildup and to prevent melting the nylon.

HOLDING
Keep in mind that nylon is not as strong as metal and can be deformed by improper chucking methods. On small accurately sized rod, use standard spring collets. On larger parts, use a 6-jaw universal chuck instead of a conventional 3-jaw chuck to distribute the holding force more uniformly. For thin walled tubular shapes, machine soft jaws so that the part is almost entirely confined.

TURNING
Satisfactory finishes can be easily obtained on nylon over a wide range of surface speeds. Use tools that are honed sharp and have high rake and clearance angles, to minimize cutting force and reduce heat build-up. Chips will be continuous and stringy. They should be directed away from the cut and prevented from winding around the workpiece. Coolants are generally not necessary for lathe work unless there is excessive heat build-up.

MILLING
Milling cutters should be honed sharp and should have high positive cutting angles. Care should be used in clamping the part to prevent distortion. Double-faced pressure sensitive tape can be used to hold down flat parts. Cutting speeds and speeds will be determined by the finish required and will be limited by heat build-up.

DRILLING
Use conventional twist drill or flat type drills. Polished flutes will aid in the removal of chips. Do not use metal cutting reamers with nylon. They do not cut freely enough. Drill small holes to size in one operation. Rough drill large holes and finish by single point boring.

THREADING
Use only sharp taps and dies on nylon parts. Don't use tools that have been used to cut metal. H5 or even larger oversized taps may be required because a threaded hole in nylon closes in when the tap is removed. Threads to close tolerances can be easily single point chased.

GRINDING
The large amounts of heat generated by grinding, together with the low heat conductance of nylon, usually dictate that liberal amounts of coolant he used in most grinding operations. Thru-feed centerless grinding of long, flexible parts of nylon can be easily accomplished, and tolerances as close as .0005" are possible. Cylindrical grinding on nylon is usually not required because it is easy to get good finishes and close tolerances on a lathe. Surface grinding of nylon is usually not necessary. If a flat surface with close tolerances and good finish are required, the best approach is fly cutting in a milling machine. No, not cutting a fly on your milling machine, FLY cutting.

STAMPING
Thin pieces may be stamped with standard equipment. Thick sections will require high shear angles if good edges are needed. Steel rule dies may be used for some parts.

MEASURING
Use ordinary measuring equipment. However, use a light touch because the material is not as hard as metal. A micrometer anvil can deform a nylon surface as much as several thousandths. Homemade, soft plug and ring gauges are useful on thin walled parts. If extremely close tolerances are involved, make SURE any temperature changes that the part will see are taken into account.

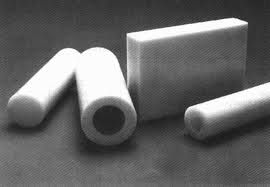


Nylon - Extruded
Very tough also at low temperatures. Moderate moisture absorption. High impact resistance. Good wear properties.

Normally used as gears, bushes, impact and vibration damping elements.
Nylon - Cast
High rigidity with good wear and crop resistance.

Normally used as gears, bushes, wear strips.
Lower and constant co-efficient of friction. Low heat build up. Less stick-slip. Longer life.

Normally used as all mechanical applications where lubrication is difficult..
Nylon - Oil Filled
we are only a phone call away
​for a price estimation
031-702-8261/2
CALL US NOW